No Bake Sand System
NO BAKE INFRASTRUCTURE
SJIF Group is a specialist in no bake castings & has a mechanised infrastructure for it. Some foundries in India use a by-pass method of no bake with no mechanisation & no reclamation which runs down the efficiency of production & quality of castings.
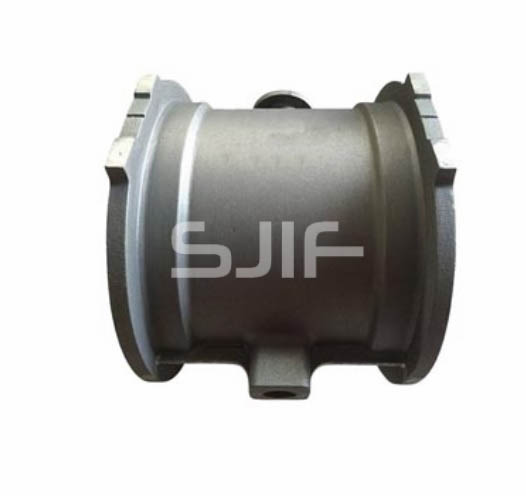
SJIF boasts of the following integrated automatic setup for no bake castings –
- 12 MT Continuous Articulated Mixer with Mitsubishi PLC
- Shakeout Unit with deck size of 2000 x 2000
- Attrition Unit
- Sand Cooler 9 MT
- Sand Classifier
- Pneumatic
- Conveying systems for dust collection
- Dust Extraction System
- Sensors & Automation at all stages
What is NO BAKE ???
“No-bake” is a casting process that involves the use of chemical binders to bond the moulding sand. Sand is conveyed to the mold fill station in preparation for filling of the mold. A mixer is used to blend the sand with the chemical binder and catalyst. As the sand exits the mixer, the binder begins the chemical process of hardening. This method of mold filling can be used for each half of the mold (cope and drag). Each mold half is then compacted to form a strong and dense mold.
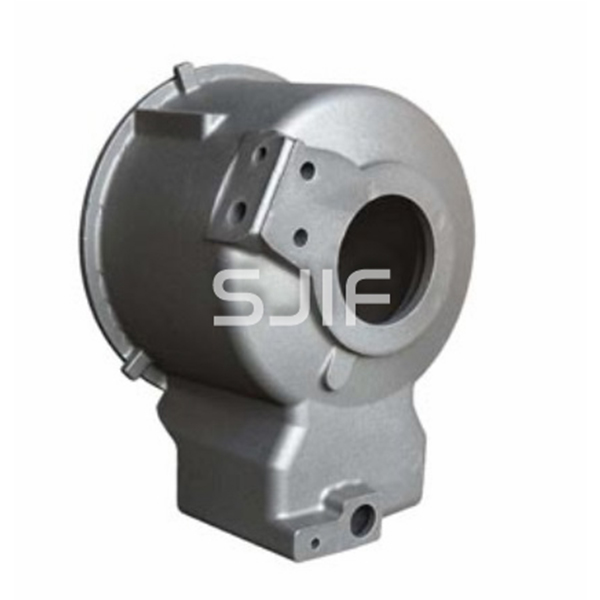
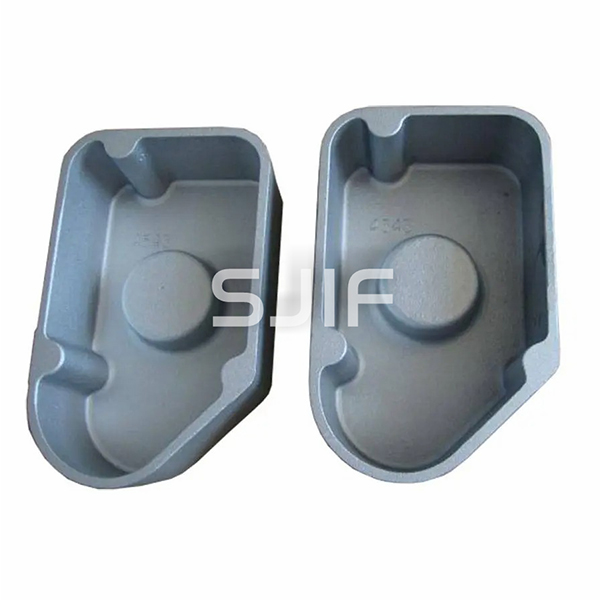
A rollover is then used to remove the mold half from the pattern box. After the sand has set, a mold wash may be applied. Cores, if required, are set into the drag and the cope is closed over the cores to complete the mold. A series of mold handling cars and conveyors move the mold into position for pouring. Once poured, the mold is allowed to cool before shake-out.
The shake-out process involves breaking the molded sand away from the casting. The casting then proceeds to a casting finishing area for riser removal, casting finishing and finalization. The broken pieces of molded sand are further broken down until the sand is returned to grain size. The sand can now be either reclaimed for reuse in the casting process or removed for disposal. Thermal reclamation is the most efficient, complete method of Nobake sand reclamation.
Range of Alloys
Virtually all metals can be cast via nobake molding with component weights ranging from less than a pound to several hundred thousand pounds. For casting designers, nobake molding offers:
Good dimensional tolerances (±0.005-0.015) because the rigidity of the mold withstands the pressures exerted by the molten metal during casting.
Compatible with most pattern materials, including wood, plastic, metal, fiberglass and polystyrene, allowing for inexpensive tooling options for casting runs as low as one. In addition, nobake molding imparts minimal tooling wear.
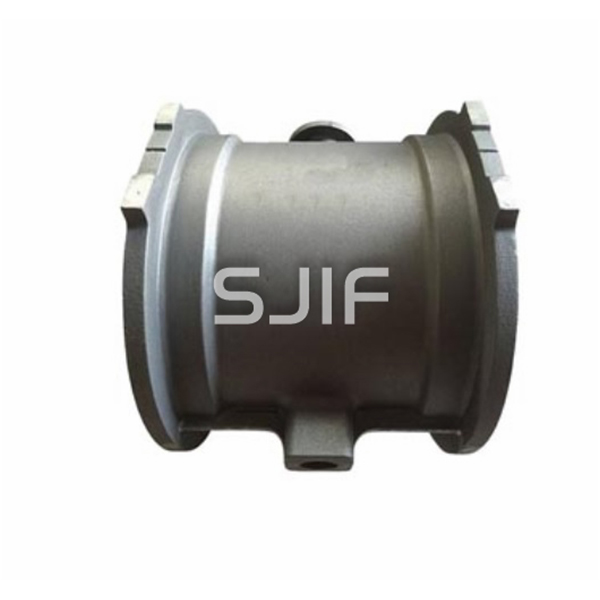
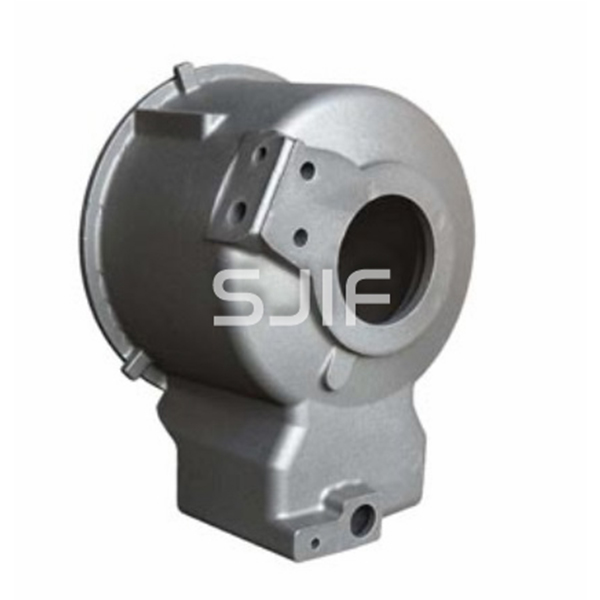
Design flexibility for intricate casting shapes. The rigidity and tensile strength of nobake molds allows for thin sections of 0.1-in. to be routinely produced. In addition, mold strength allows for minimal draft and radii requirements in casting design.
Reduced opportunity for gas-related defects as the nitrogen content of most binder systems used for nobake molding minimize susceptibility to gas porosity.
Ability to work well with unique metal casting quality enhancement tools such as metal filters, ceramic runner systems and exothermic risers to improve casting properties.
Fine surface finishes that can be upgraded further with the mold and core coatings to support special finishing on the cast components such as paint or dressing. In addition, nobake casters can alter their molding media make-up from basic silica sand to higher-end media such as chromite or zircon sand for applications requiring X-ray quality and extreme pressure tightness.
Low to medium volume production capability with runs from 1-5,000 parts per year.
The key, as with any casting process, is to ensure the casting design is optimized to take advantage of the benefits afforded by no – bake molding.
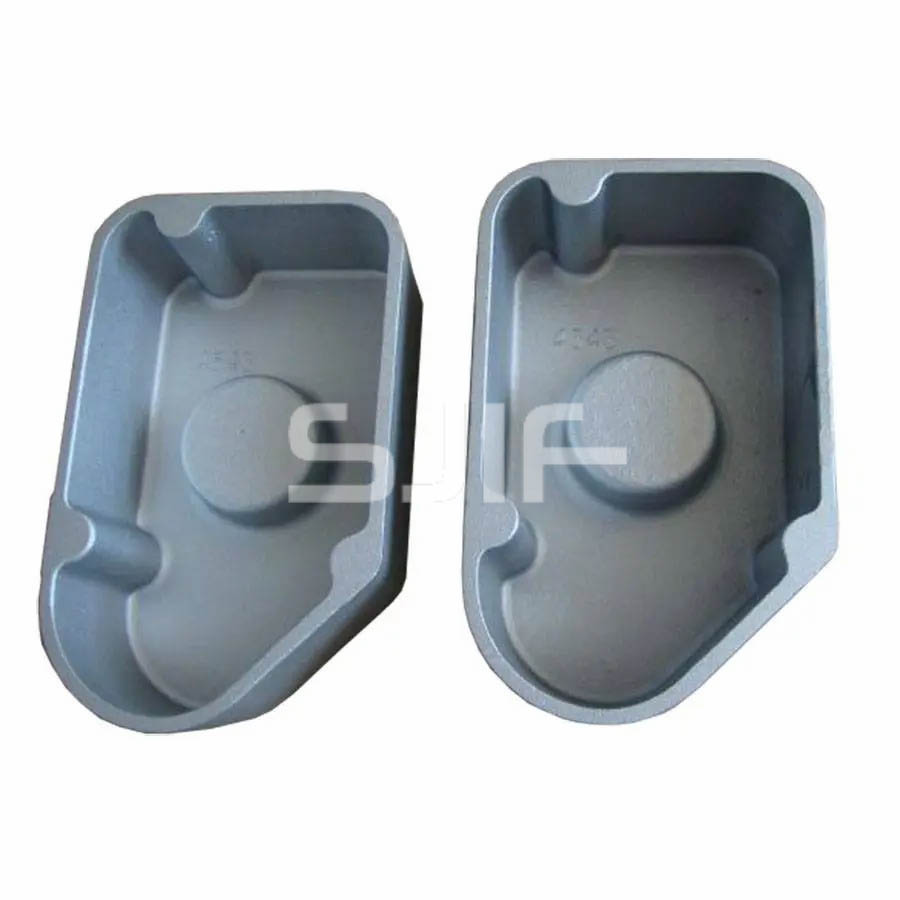